This article explains V-belts, covering their definition, various types, design aspects, advantages, and extensive applications in industries like automotive and machinery. It highlights their efficiency, flexibility, and low maintenance, making them critical for effective power transmission. Additionally, the blog provides insights into how to select the right V-belt for specific needs.
Key Highlights
- Comprehensive explanation of what a V-belt is and its significance in power transmission.
- Detailed categorization of V-belt types (classical, narrow, cogged, etc.).
- Insights into the design elements that enhance efficiency and performance.
- Overview of the benefits, such as durability, flexibility, and ease of maintenance.
- Real-world applications across diverse industries, including automotive and manufacturing.
- Tips for selecting the right V-belt for specific requirement
Overview of V-Belt
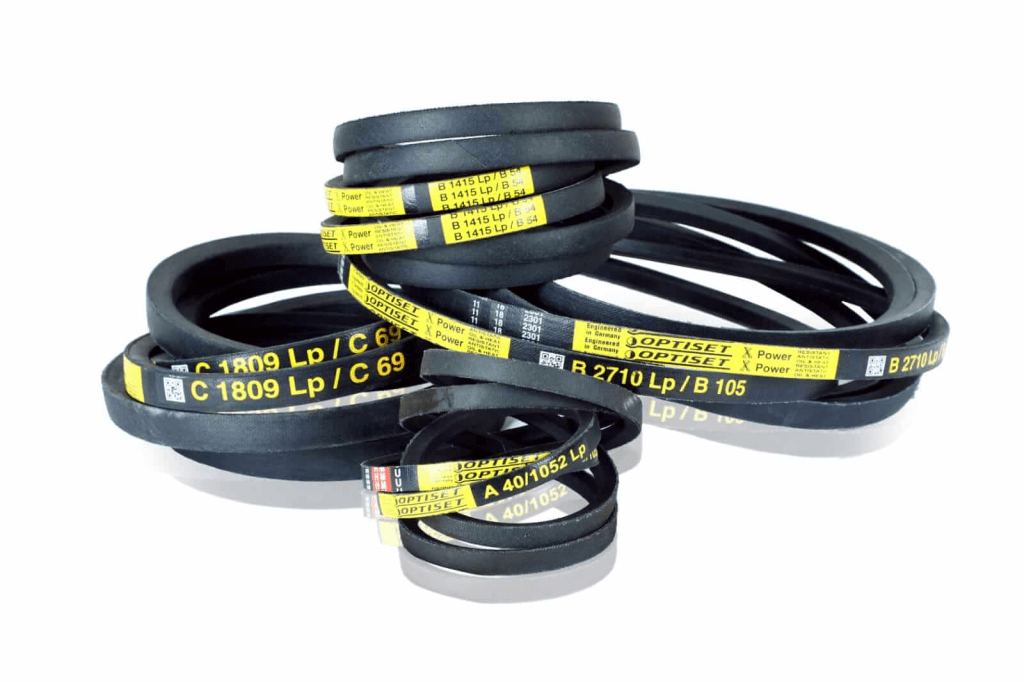
V-belts facilitate the smooth transfer of mechanical energy in machines like power highways. Consider the engine of your car, which powers the air conditioning, power steering, fan, and alternator. These belts come in different sizes and have a trapezoid shape. Their firm hold on pulleys is essential for avoiding slips and guaranteeing dependability. This quick guide simplifies V-belts, focusing on their build, types, and main uses. Whether you’re into cars or machines, this overview will ensure you understand V-belts’ fundamentals. So, grab a seat and get set for a leisurely ride through V belt drives!
What is a V-Belt?
A V belt is a flexible power transmission device that effectively transfers energy from one shaft to another. Its trapezoid-like form ensures a tight fit and a secure connection when it slides into the shaft sheaves’ grooves. Because of its unique construction, the tensioned V Belt can wedge firmly into the sheave grooves, causing friction and transferring more torque without slipping and losing power.
V belts are natural rubber, giving them flexibility and breathability. This allows them to be bent around sheaves. They are robust due to the trapezoid-shaped twisting of their fibrous tension chords. In specific designs, cogs help reduce operating temperatures and enhance leaning resistance. The V belt is a crucial component of V belt drive systems because it offers dependable power transmission between shafts, durability, and efficiency in various applications.
Features of V-Belt
V belts are a reliable and flexible option for power transmission because they offer durability, efficiency, and compact design. Their simple design and minimal maintenance requirements make them an excellent choice for various applications, from industrial machinery to automobile engines. Listed below are the features:
- Efficient Power Transmission: The V belt’s trapezoidal shape maximizes power transmission efficiency, up to 98%, by providing a firm grip on pulleys and reducing slippage.
- Compact Design: They take up less room when comparing V belt drives to systems like gear drives or flat belts. They can move around smaller pulleys because of their flexibility.
- High Load Capacity: V belts are dependable for various applications because of their robust design and positive engagement with pulleys, enabling them to handle heavy loads.
- Shock Absorption: V belts can absorb shock loads because of their flexibility, which acts as a buffer to protect equipment and stop damage.
- Low Maintenance: Due to their lack of lubrication needs, V-belts are low-maintenance and provide engineers and mechanics with an easy-to-use solution.
Types of V-belts
There are two primary classifications for V-belts: types based on dimensions and types based on construction. Various V-belt options exist in the market, such as classical v belts, v belt a section, narrow v belts, cogged v belts, raw edge cogged belts, banded v belts, etc. Each type has characteristics that suit applications, allowing it to be flexible to cope with a wide range of industry needs. To understand their specific applications in machinery, we shall study each type in detail.
V- Belt Types Based on the Dimension
- Standard V-Belts:
These belts are available in types A, B, C, D, E, and Z, as shown in Table 1, and are frequently used in power transmission. Each is a different size for a different use.
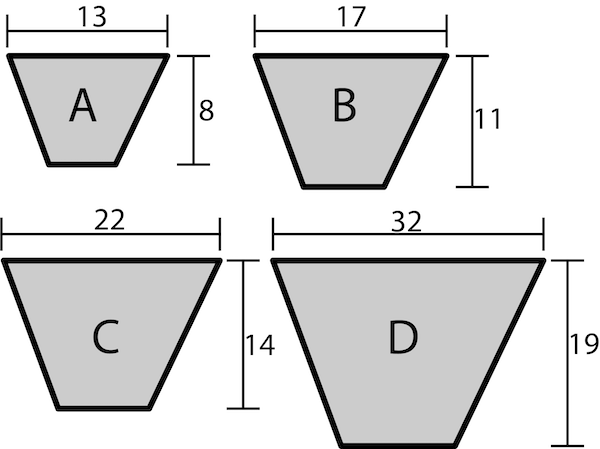
Image Source (Tameson)
Table 1: Standard v-belt dimensions

- Wedge V-Belts:
Wedge v-belts, ideal for compact spaces, require fewer belts due to a higher power rating. They manage 1.5 – 2 times the load of standard v-belts with an identical top width. These belts offer exceptional strength in motion, featuring a 40-degree angle and a top-to-width ratio of 1.2:1. Common designations, as detailed in Table 2, include SPZ, SPA, SPC, and SPB.
Table 2: Wedge v-belt dimensions
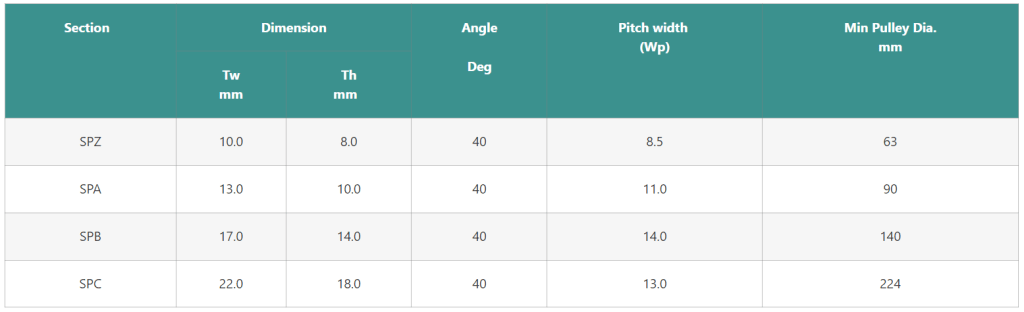
- Narrow V-Belts:
Narrow v-belts, perfect for managing substantial loads effortlessly, come in standard designations such as 3V, 5V, and 8V. These belts are standardized and widely employed in North America. To ensure a secure fit, it is recommended to match 5V with SPB pulleys and 3V with SPZ pulleys, as detailed in Table/Figure 3.
Table 3: Narrow v-belt dimensions
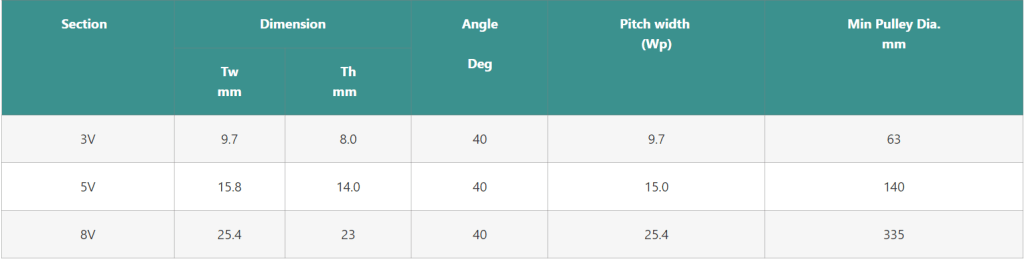
- Double or Hexagonal V-Belts:
Hexagonal V-belts, known as double v-belts, boast exceptional flexibility. Featuring steel wires running through the centre, these belts can bend in any direction, making them ideal for systems with pulleys moving opposite. Look out for typical labels such as AA, BB, and CC, as indicated in Figure 4.
- Banded V-Belt:
A banded v-belt, formed by connecting multiple v-belts in parallel with a top band or cloth cover, proves exceptionally robust in high-power applications. The v-belt section number and an H, such as HA, HB, HSPA, HSPB, etc., can identify these belts, as detailed in Figure 5.
- Fractional Horsepower V-Belts:
Light and efficient, fractional horsepower v-belts are for small tasks like machines in shops or household appliances needing one horsepower or less. Consider that the sizes of 2L, 3L, 4L, and 5L correspond to the width of the belt.
- Cogged V Belt:
Cogged v belts stand out with notches on the bottom, allowing flexibility around smaller radii. They’re not entirely covered by a fibre cover, unlike other types. Examples of the cogged belt are ZX, AX, 3VX, and many more, with an X after the v belt section number. Cogged wedge belts shall be listed as XPA, XPB, etc.
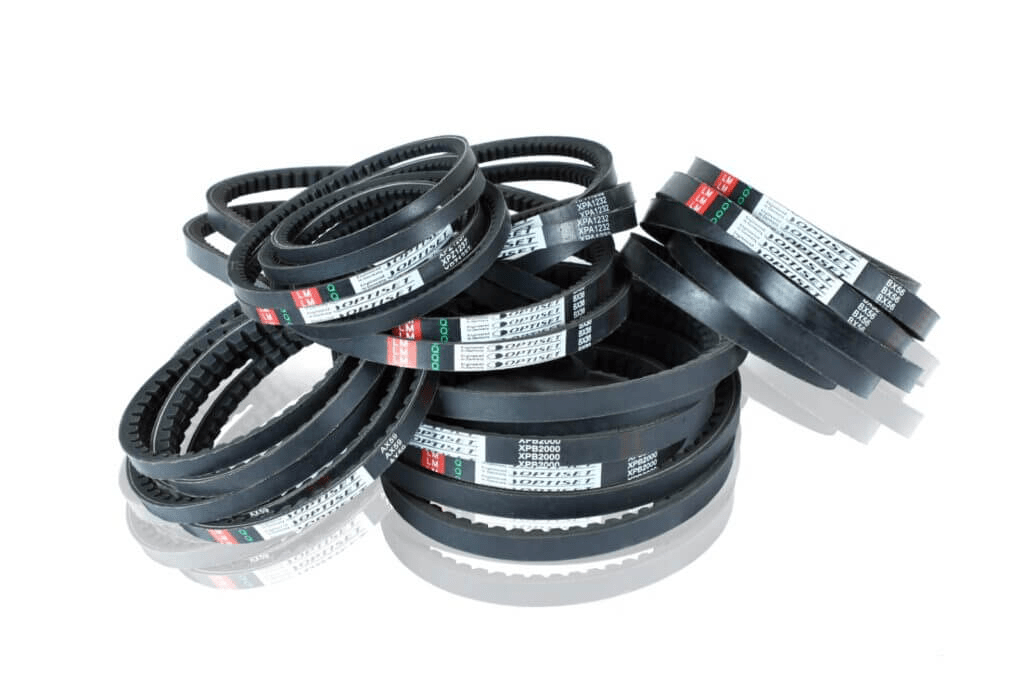
- Double Cogged V-Belts:
Double-cogged v-belts bring together the flexibility of cogged and hexagonal v-belts. Ideal for applications needing a bendy belt and a small radius. The top cogged structure allows it to move like a zigzag, making it great for multiple pulleys. Sizes vary based on manufacturer standards.
- Cogged V-Belt vs. Standard V-Belt:
Cogged belts bend sharper with notches at the bottom, are more durable, produce less heat, and have higher efficiency than standard v-belts.
- Poly V Belt:
Because of their non-standard section dimensions, these belts are more flexible than banded V-belts. They are thin, multi-groove belts. Designations like PH, PJ, PK, PL, and PM categorize Poly V belts, making them ideal for driving multiple pulleys in various applications.
V- Belt Construction Based on their types
Based on their construction, V-belts are divided into two primary categories:
- Wrapped V-belts
- Raw-Edge V-belts
- Wrapped V-Belts:
These V-belts are entirely covered, either with plastic or fabric. They function quietly, are extensively used, and resist the elements strongly. However, they have a cost because low friction increases the possibility of slippage, reducing power. Despite this, wrapped v belts function effectively when a certain amount of slippage is acceptable without compromising the belt.
- Raw Edge V-Belts:
These belts are made without an outer covering. These belts increase friction and decrease slippage by directly connecting the material and the pulley’s surface. Their rubber core is resilient, withstanding abrasions better than their covered counterparts. Additionally, raw edge v-belts can be divided into three primary groups:
- Raw Edge Plain (REP):
Depending on the design, the bottom may or may not have a cover and features layers of fabric or plastic on top.
- Raw Edge Laminated (REL):
These are like REP but have extra laminated fabric layers at the centre to reduce operating noise.
- Raw Edge Cogged (REC):
These v-belts, also called raw edge notched v-belts, improve flexibility and have notches on the bottom side. They perform well at dissipating heat, which makes them appropriate for high-temperature applications and ideal for smaller pulleys.
Design and Selection Consideration for V-Belts
Selecting the right V belt for a system involves considering various factors to ensure optimal performance. The following are the essentials to keep in mind:
Application:
- Choosing the right v belt for a system involves considering factors like operating speeds, intermittent or continuous operation, belt efficiency, layout (e.g., serpentine or quarter turn), misalignment tolerance, transmitted power, and exposure to harsh conditions (such as extreme temperatures, abrasives, ozone, and oils).
- Industry professionals can select from various v belts, from light-duty to heavy-duty industrial options, based on the critical factors for their specific needs.
Profiles:
V belts come in various profiles or cross-sections, each with its unique dimensions. The primary industry standards include:
- Classical: Developed in the 1930s, the classical standard offers six sizes (A, B, C, D, E, and Z).
- Narrow: Narrow v belts, with steeper sidewalls than the classical standard, boost wedging and load-carrying capacities and are offered in three sizes (3V, 5V, and 8V).
- Metric: Complying with international standards like ISO and DIN, the metric standard (e.g., XPZ SPZ, XPA SPA, XPB SPB, XPC SPC, 10X, 13X, and 17X) is suitable for machinery belts used globally.
- Fractional Horsepower: The fractional horsepower standard’s 2L, 3L, 4L, and 5L sizes are meant for light-duty applications.
These profiles may also be found in raw-edge cogged variations to enhance specific performance characteristics.
How Do V-Belts Work?
V-belts operate through a simple yet effective mechanism, with critical components in play:
- Base Rubber Compound: The primary material forming the V-belt, this rubber acts as a shock absorber during operations.
- Tensile Members (Cords): Embedded in the rubber, these cords strengthen the V-belt, enabling it to transmit power efficiently.
- Protective Covering: A textile cover ensures the V-belt maintains the proper grip for power transmission while safeguarding the rubber from frictional damage and external contaminants.
These components work together in wrapped v belts, effectively transmitting power and torque between pulleys through friction-based means.
Uses of V-Belt
V-belts play a crucial role in various applications due to their versatility. Here are some critical uses:
- Agricultural Equipment: V-belts are used in tractors, combines, and mowers in the farming industry to power pumps, fans, and other devices.
- Automobile Engines: Car engines frequently use V-belts to drive accessories such as the air conditioning compressor, water pump, power steering pump, alternator, and compressor.
- Appliances: V-belts drive parts like the agitator or drum in common household appliances like washing machines and dryers.
- Industrial Machinery: V-belts are commonly used in drilling presses, lathes, mills, conveyors, and compressors to transfer power from motors to various machine parts.
Overview of Belt Drive
A belt drive is a primary mechanism for transferring power between rotating shafts with parallel axes. This system creates tension through belts looped over pulleys attached to driver and follower shafts. This process’s friction enables the belt to grip the pulley while operating.
The driver pulley’s rotation tightens the tight side of the belt, which causes the follower pulley to experience a tangential force that causes torque to be applied to the driven shaft. Alternatively, the slack side displays less tension.
There are many types of belt drives; older models include flat belts of cloth or leather. The original flat belts drive had slipping problems at higher loads and speeds, even though they were ideal for low-power applications like farming and logging. In response to these difficulties, modern technology has developed thin, effective flat belts composed of cutting-edge materials like polyester, aramid fabric, or polyamide, which improve performance and durability.
Rope drives made of cotton or hemp were an early substitute that solved pulley climbing problems and opened the way for round belts made of elastomeric materials like rubber, nylon, or urethane.
The emergence of robust elastomeric materials, such as synthetic and natural rubber and different polymers, represented a significant breakthrough in belt materials. Because of these materials, belts in belt drives can endure continuous stress and torque. Timing belts, V belts, ribbed belts, and multi-groove belts were created as a result, providing solutions for previous belt drive issues.
Advantages and Disadvantages of V-Belt drive
Advantages of V-Belt drive:
- Smooth and Quiet Operation: V-belt drives ensure the pulley and belt run smoothly and silently, which helps create a quieter workplace.
- Compact Design: The V-belt drive’s small pulley center spacing allows for its compact design, making it ideal for limited spaces.
- Negligible Slip: These drives improve power transmission and efficiency by having little slip between the belt and pulley.
- Versatile Orientation: V-belt drives offer adaptability in installation as they can operate with horizontal, vertical, or inclined axes.
- Vibration Dampening: The ability of V-belt drives to reduce vibrations makes machinery operation more stable and smoother.
Disadvantages of V-Belt drive
- Limited Distance Application: V-belt drives are inappropriate for long-distance applications because of their higher weight per unit length.
- Synchronous Machines: These drives are not free from creeps, so they cannot be used with synchronous machines.
- Speed Limitations: V-belts are inappropriate for speeds higher than 50 m/s or lower than 5 m/s because of centrifugal tension.
- Complex Pulley Construction: V-belt pulley construction is more intricate than flat belts, further complicating the system.
Application of V- Belts
V-belts are widely used in various industries, demonstrating their adaptability and effectiveness in powering multiple devices and machinery. Among the noteworthy applications are:
- Drills: V-belts are essential for driving drills because they supply the torque and power required for effective drilling operations.
- Light-Duty Milling Machines: V-belts are a popular option for powering these machines when precision and dependability are crucial.
- Power Tools: V-belts are used by many power tools, such as saws and grinders, to transfer power efficiently and provide maximum performance.
- Agricultural Machines: V-belts are used in tractors and harvesters, among other equipment, to ensure the smooth operation of these vital devices.
- Industrial Fans: Industrial fans are essential for cooling and ventilation. To transmit power and keep the airflow constant, they frequently rely on industrial v belts.
- Woodworking Equipment: V-belt mechanisms, such as table saws and wood lathes, are commonly used in woodworking equipment to ensure efficient power transmission.
Conclusion
V-belts are vital power transmission components used extensively in many industries. Their trapezoid shape ensures Effective energy transfer, with a rubber base, tensile members, and a protective covering. V-belts are essential for industrial machinery, home appliances, automotive engines, and more because of their compact design and smooth operation. Despite their drawbacks, their versatility and dependability make them essential for powering industrial fans, drills, tools, and agricultural machinery. V-belts are essentially small, powerful, and silent parts that power the machinery that moves our world.
FAQs
What is the V-belt used for?
V-belts are used to transmit mechanical power between different parts of a machine efficiently.
What is the summary of belt drives?
Belt drives offer a cost-effective solution for transmitting mechanical power, particularly in applications with widely separated or nonparallel shafts. They serve as an economical alternative to gears and play a crucial role in various systems, including V belt drive, flat belt drive, and other industrial v belts like banded v belts and cogged v belt.
What is the main function of V-belts?
V-belts play a crucial role in machines by efficiently transferring mechanical power between different components, ensuring seamless operation.
What are the factors considering the design of belt?
When designing a belt, essential factors to consider are:
- Power transmission requirements
- Shaft separation
- Service environment
- Space constraints
- Type of driven load
- Speed ratio
What is the application of v belt?
V-belts are applied in industrial settings based on operating speeds, layout preferences, and exposure to harsh conditions. This ensures optimized performance in both light-duty and heavy-duty industrial applications.
What are all the types of V belts?
There are several types of V-belts, including Fractional horsepower v-belts, Poly v-belts, Cogged v-belt, Double Cogged V-Belt, Banded v-belt, Standard v-belt, Wedge v-belts, Narrow v-belt. Each type serves specific purposes, offering versatility in power transmission applications.
- v belt drive 12
- V belt 19
- flat belt drive 1
- V-belt 46
- industrial v belts 2
- v belt 17
- banded v belts 2
- poly v belt 2
- cogged v belt 4
- cogged belt 2
- raw edge cogged belt 1
- v belt a section 1
- Optiset V Belt
V-belts are indispensable in modern machinery due to their efficiency, versatility, and cost-effectiveness. Their varied types and designs cater to a wide range of applications, ensuring optimal performance across industries. Proper selection and maintenance of V-belts can enhance machinery life and reduce operational costs, making them a preferred choice for power transmission solutions.